Unruly
and abusive passengers are getting a lot of media attention these
days for their disruption of commercial flights. But ASRS also hears
about unsung passenger heroes whose vigilance is responsible for
bringing hazards to the attention of the crew. From holes to leaks
to dings, passengers can provide early warning of aircraft equipment
problems that might otherwise escape detection until a serious hazard
develops. Some recent examples from ASRS files:
- During
taxi for takeoff, a storm passed over the field. When the storm
had passed we departed. During the storm, pea-sized hail fell
intermittently. A passenger deplaning [at destination] remarked
that there were dents and holes in the "flaps." Maintenance
was immediately notified and confirmed the passengers
observation.
In other cases,
the timing of passenger input can pose a credibility problem for
the flight crew:
- Just
prior to takeoff, Flight Attendant notified us that a passenger
thought he may have seen a hole in one of our turbine
blades. This seemed impossible, as the engines were running
at this time and a hole would be impossible to see.
After getting more information from the Attendant, the passenger
stated he had seen this hole prior to engine start. Since 10
minutes had elapsed from engine start until the passenger actually
said anything about this, it seemed illogical. If a passenger
was truly concerned, it seemed they would have mentioned it
immediately... Cockpit crew decided this was probably just another
passenger "crying wolf" and elected to continue takeoff.
All engine parameters were normal during the 2-1/2 hour flight.
Subsequently, during ground inspection following flight, [maintenance]
found 2 turbine blades on the left engine with nicks in them.
Lesson learned: sometimes a passenger may actually know what
they are talking about and we need to consider this information
pertinent and act accordingly.
Another incident
shows how passenger observation can be a safety factor during
crew swaps and aircraft changes.
- On
descent, we were advised by our company that we would have an
unscheduled aircraft change [at destination]. When we arrived
at our new aircraft, the Captain I was trading aircraft with
advised me that the autopilot was inoperative. He also told
me that a passenger had observed fluid coming from the right
wing. He said he had called contract maintenance to inspect
the wing. The other Captain then...wrote a discrepancy in the
aircraft logbook describing what the passenger had seen, then
departed to the aircraft that we had left at another gate. Approximately
10 minutes later, the mechanic came to the cockpit and informed
me that there was fuel in a dry bay area on the right wing.
I called our company maintenance control office and had the
mechanic explain what he had found. After he had finished, our
maintenance office informed me that the aircraft was Out of
Service...
Any leak in
the forward wing upper surface pylon attach area is serious. The
"other" Captain took the correct actions in documenting
the problem and having the reported fluid leak checked.
Emergency
Connections
The problem
with new technology is that it often works in unexpected ways
or not at all. An air carrier Captain offers a thoughtful commentary
on how an onboard medical emergency might have been more smoothly
handled.
- Medical
emergency at 12,000 feet MSL on STAR [arrival]. Lead Flight Attendant
advised flight deck crew that a 10-year-old boy was experiencing
an apparent severe allergic reaction. The Flight Attendants were
being assisted by a Registered Nurse and wanted to administer
[antihistamine]. Our new cabin "airphone" medical clinic
contact did not work. I contacted our Flight Dispatcher on the
radio and requested a phone patch to medical clinic.
ATC was advised of our problem. We were now well into the approach
phase below 10,000 feet, with the usual altitude and heading changes.
We were IFR in the clouds. ATC assigned us Runway 30L to facilitate
our arrival. I began to reprogram the approach...since we were
initially assigned 30R. Considerations were getting the airplane
on the ground safely and quickly, obtaining clinic concurrence
prior to administering the drug, [and] making sure both pilots
were attending to primary tasks.
I set up the observers jackbox and had the Flight Attendant
talk to the clinic on the #2 radio. This resulted in two inexperienced
radio operators attempting to converse with each other. The process
took too long, but the end result was satisfactory. If I had this
situation again, I would use the Dispatcher to relay information
to the [clinic] and then back to the aircraft...
A possible drawback
to using Dispatch to relay medical information is that ground-based
medical personnel might find it difficult to evaluate indirect information.
If time and equipment permit, a phone patch between assisting onboard
medical personnel, Dispatch, and ground-based clinicians might be
the most effective means of communication during an inflight medical
emergency.
The
Hurry-Up
Syndrome Revisited
Past ASRS research
has documented that the "hurry-up syndrome" any situation
in which pilot performance is degraded by a perceived or actual need
to rush the completion of cockpit tasks often results in downstream
safety incidents. In practical terms, this means that omissions or
oversights made during pre-flight and taxi-out often manifest themselves
during takeoff and departure.
A cargo pilots
report to ASRS shows how the hurry-up syndrome and complacency can
lead even an experienced pilot to make a novices error
in this case a wrong-direction departure:
- The
departure ATIS was calling for departure on Runway 8L. I was cleared
to taxi and hold short of 8L at intersection D for intersection
departure behind company jet traffic. Tower cleared me for takeoff
and I proceeded to turn onto the runway and started takeoff roll.
At approximately 500 feet AGL, Tower informed me I had departed
Runway 26R and to turn right to 360° and then on course. No
traffic conflicts occurred, and there was no shortage of runway
as taxiway D is at the midpoint of a 10,000-foot runway.
From the beginning of the taxi for takeoff, I was rushing for departure
and preoccupied with my departure preparations. I was late and the
weather was moderately low, all factors that increased my anxiety
and haste to depart. I am very familiar with the airport and I believe
this allowed complacency to set in. The departure from midfield
made it difficult for the ATC controller to anticipate my mistake...
[Also] the company jet did not take off in front of me, but crossed
Runway 8L/28R on the way to the south set of runways. No other aircraft
were taking off or landing, which would have warned me of my mistake.
1. Allowing oneself to be rushed increases chances for mistakes
to happen and go unnoticed
2. Be suspicious and think through intersection departures. Check
heading indicator on line-up to verify departure runway. Slow down
to allow the controller to stay in the loop and help avoid mistakes.
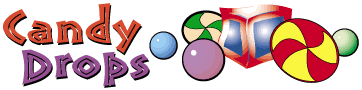
As colorful stockpiles
of candy in grocery store aisles signal the approach of Halloween and
other fall holidays, several ASRS reports remind us that confections
in the cockpit may not always bring sweet endings. From a GA pilot whose
"candy drop" turned into a real dud:
- Events
began with a descent into Low Altitude Flight (1000 feet AGL) in
order to fly close to a family outing. This was at my familys
farm which was out in the country, and I desired to drop a bag of
candy out as fun gesture. After 3 passes, I proceeded to turn for
a 4th and dropped to 500 feet AGL in order to make the drop... After
the drop was made and all was clear, I proceeded to add full throttle
to depart and to land at [home] field. The adding of full throttle
only produced a maximum 1800 RPM. I pulled carb heat, applied full
mixture, full throttle, and checked mag position. I was unsuccessful
with power recovery and now was descending below 500 feet AGL. Power
lines and trees became a big concern. I cleared powerlines easily
but brushed the top of the trees. At this time I knew a forced landing
was needed. I proceeded to land in the nearest pasture, making a
clean landing. Once I had completely stopped the airplane, I called
ATC to inform them of my location and good condition...
I had a certified mechanic do a thorough check of the engine and
structure... The mechanic informed me that the aircraft was in normal
condition and airworthy... I feel that the conditions leading up
to the forced landing are now clearer. Even with temperatures over
85°F, the high humidity and slower flight led to carburetor
icing... Application of carb heat started to occur but without much
altitude, [and] there was not sufficient time for the ice to melt.
Advice from the
School of Experience: "Fly the airplane first."
Another GA pilot
who experienced engine problems and an off-airport landing also reported
a candy connection:
- ...Approximately
2-3 minutes after going through 4700 feet to 5500 feet, the engine
quickly lost RPM... I attempted to restart, checked fuel shutoff,
checked throttle, checked mixture, checked ignition, checked carb
heat. After following these procedures, I had to make an off-airport
emergency landing in a farmers field. Pilot and passengers
suffered no injuries... I believe a bag of candy sitting over fuel
shutoff valve on floor between seats may have inadvertently shut
off or restricted [fuel] flow in some way. However, fuel valve was
on when checked during restart procedures.